1 Introduction
In this paper, according to the characteristics of PID control, an integral separation control method is designed, that is, when the system error is large, the integral link is cancelled to avoid the system overshoot due to integral accumulation; when the system error is small, the integral link is introduced To eliminate errors and improve control accuracy. This integral separation PID control is applied to the real-time position control of the AC servo system, so that the static and dynamic performance indicators of the control process are ideal.
2 System structure design
Integral separation PID control AC servo system structure is shown in Figure 1. In the figure, θd is the given angular displacement, θ is the actual angular displacement of the motor shaft, and e is the deviation obtained by comparing θd and θ, then:

In Figure 1, u is the expected speed of PID control; ωd is the desired motor speed; ω is the actual motor speed; the deviation of ωd and ω generates the desired motor electromagnetic torque Td through the speed regulator. Due to the lack of the inner loop, it can be controlled by the outer loop To compensate, so the speed regulator can use the general PI regulator, and the electromagnetic torque control of the motor uses a direct torque control method.
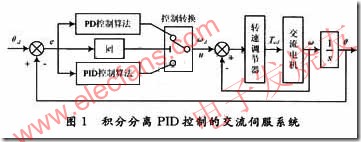
3 Integral separation PID controller
PID control is a mature and widely used control method with a simple structure and good control effect for most processes. The discrete PID control law is:

In the formula, u (k) is the output of the controller at time k; KP, KI, KD are the proportional coefficient, integral coefficient and differential coefficient; e (K) is the difference between the position of the AC servo system at the current time and the expected value; e (k-1) is the difference between the position of the AC servo system at the last sampling time and the expected value.
From equation (2), the increment between the controller output u (k) at the k-th cycle and the control quantity u (k-1) at the k-1 cycle is:

In PID control, the role of the integration link is to eliminate static errors and improve the control accuracy of the system. If the integration link is introduced in the initial stage with large errors, it will cause: the accumulation of PID points, which will cause a large overshoot of the system. Therefore, according to the characteristics of PID control, this paper designs a control method of integral separation. The program block diagram of integral separation PID control algorithm is shown in Figure 2.
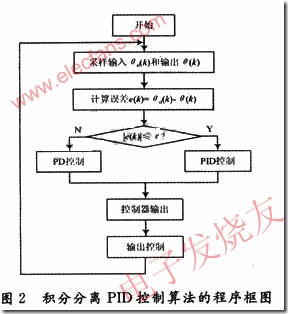
When the system error is large, the integral link is cancelled, and PD control is adopted to avoid large overshoot of the system due to integral accumulation; when the system error is small, the integral link is introduced and PID control is adopted to eliminate the error and improve the control accuracy. which is:
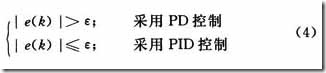
In the formula, ε> 0 is the artificially set threshold.
The integral separation control algorithm can be expressed as:

In the formula, T is the sampling time, a is the switching coefficient of the integral term, namely:
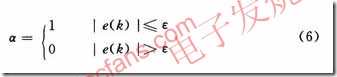
4 Experimental research
The AC motor parameters used in the experiment are Pn = 2.2 kW, Un = 220 V, In = 5 A, nn = 1 440 r / min, r1 = 2.91 Ω, r2 = 3.04 Ω, Is = 0.456 94 H, Ir = 0.456 94 H, Im = O.444 27 H, Ten = 14 N.
Experiments show that the integral separation PID control fully utilizes the advantages of PID control with high adjustment accuracy and improves the control accuracy of the system.
5 Conclusion
In this paper, an AC servo system based on integral separation PID control is proposed. When the system error is large, the integration link is cancelled; when the error is small, the integration link is introduced to make the system's static and dynamic performance indicators ideal. This control method improves the accuracy of the system. Simulation experiment results show that the controller has very good dynamic and static performance and is an effective controller.
Single Phase Ac Motor,Ac Single Pole Motors,Single Phase Motor,Single Phase Motor Connection
Changzhou Sherry International Trading Co., Ltd. , https://www.sherry-motor.com