Introduction: HPM75 non-magnetic steel with high hardness, wear resistance, corrosion resistance and non-magnetic properties comparable to stainless steel SUS304 and many other mold characteristics; therefore the most suitable for corrosion resistance and wear resistance of the mold product.
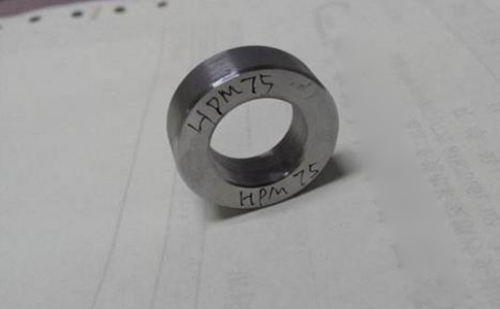
1, HPM75 non-magnetic steel
HPM75 is a non-magnetic, high hardness, easy-to-cut plastic mold steel produced through a special melting process. It is a non-magnetic, high-strength, austenitic, non-magnetic mold steel in HPM series steel. It maintains stable austenite in all conditions and has a very low magnetic permeability. HPM75 non-magnetic steel has the characteristics of high hardness, wear resistance, corrosion resistance and non-magnetic properties comparable to stainless steel SUS304 and many other mold characteristics; therefore, it is most suitable for mold products that require high corrosion resistance and wear resistance. Gas nitrogen carbonitriding heat treatment can further increase the surface hardness and wear resistance, thereby increasing the service life of the die. HPM75 non-magnetic steel is prone to work hardening and low speed machining is recommended.
2. Introduction of HPM75 non-magnetic steel heat treatment process
The heat treatment process mainly includes: a high temperature annealing process, a solid solution softening process, and a age hardening process; they are as follows:
(1) High temperature annealing process
The hardness of the mold material is high, and its mechanical processing performance is poor; the purpose of the high temperature annealing of the mold is to improve the mechanical processing performance, eliminate the forging stress, facilitate the mold manufacturing and processing, and shorten the processing cycle; the annealing process flow: annealing temperature 870-890°C, heat preservation 3 - 6h, the cooling rate from the annealing temperature to 500 °C should be controlled, the cooling time should not be less than 6 hours, hardness: 28-30HRC.
(2) Solid solution softening treatment process
The solid solution process is to dissolve the material carbides into the matrix, prepare for age hardening treatment, and also improve the cutting performance. It is also called softening treatment in the production; the equipment used: box-type electric furnace (preheating), high-temperature salt Bath furnace (solid solution) or box type high temperature electric furnace;Solid solution softening treatment process: When the balance is more than 1.5-2mm, use high temperature box furnace for solution heating, heating temperature 1150-1180°C, salt bath furnace insulation 15- * 20min / mm, box furnace insulation 30min / mm, water-cooled, HPM75 solid solution hardness 20-22HRC, material microstructure: austenite + undissolved primary carbide.
(3) Age hardening treatment process
The age-hardening treatment after the mold manufacturing process is to disperse carbides dissolved on the substrate to deposit on the substrate, thereby strengthening the matrix, increasing the hardness and wear resistance, also called hardening treatment in the production; using the box-type electric furnace, aging temperature 650-700 °C, aging 15-20h, water-cooled or air-cooled, hardness up to 45-50HRC.
3, using HPM75 non-magnetic steel mold making process
(1) Process flow: Forging - high temperature annealing - roughing - solution softening - semi-finishing - age hardening - finishing - nitriding.
(2) HPM75 material heat treatment characteristics Surface: This material is through the secondary hardening method to increase the hardness, in addition to this material itself is more viscous, resulting in the tool is easy to wear; In the solution after the softening process Machinability Effectively improving and then processing the appropriate coolant will help ensure the size of the semi-finishing process, as well as the drilling and threading of small holes. The finishing after age-hardening treatment is the last mechanical processing step. For the mold to be nitrided, it is necessary to adjust the size. Nitriding is to further improve the surface hardness, wear resistance and service life of the mold, and to improve the blank Mold release, blank quality and production efficiency.
4. Nitriding process of the mould made of HPM75 non-magnetic steel (surface nitriding treatment process)
(1) Test materials: HPM75 non-magnetic steel chemical composition is as follows:
C Si Mn PS Cr Mo VW
0.69 0.65 15.3 0.02 0.01 2.31 0.75 1.83 0.62
Note: The material state is solid solution + aging, hardness is 47HRC.
(2) Test method: The test was conducted using 8mm*15mm*30mm specimens, respectively, in a LD50 ion nitriding furnace and an RN35 gas nitrocarburizing furnace, and the depth of the penetration layer was measured by hardness shaving method.
Results and analysis: The surface hardness of ion and gas nitriding was 1130HV0.3 and 1180HV0.3 respectively, and the total depth of the layers was 0.21mm and 0.15mm, respectively. The substrate hardness of both nitriding processes is 490HV0.3.
The life of the mold treated by the two nitriding processes was 3.2 times and 2.3 times longer than that of the solid solution + aging state, respectively. HPM75 non-magnetic steel contains more alloying elements, these elements combined with nitrogen, making the mold surface with high hardness and wear resistance, which greatly increased the life of the mold.
5 Conclusion
(1) The correct use of HPM75 non-magnetic steel heat treatment process and the process flow in the mold processing, is conducive to the processing and normal use of the mold.
(2) Gas nitrocarburizing significantly improves the surface hardness, wear resistance, and service life of HPM75 non-magnetic steel molds. The surface of the blanks pressed with it is bright and easy to release, which improves the quality and production efficiency of the blanks.
(3) Nitriding does not change the non-magnetic properties of HPM75 steel.
Electronic Cigarette,Largest E-Cig Oem,China E-Cig Oem,Vape Pen Oem,Vape Device Oem
Shenzhen MASON VAP Technology Co., Ltd. , https://www.disposablevapepenfactory.com