Electronic enthusiasts eight o'clock: After the consumer electronics market such as smart phones tends to be flat, automotive electronics has become the next hot spot for the electronics industry. As can be seen from the annual reports of several major semiconductor manufacturers in the industry in 2016, for example, in 2016, NXP’s automotive electronics revenues were $3.379 billion, accounting for 35.6% of its total revenue. The main revenue of Feiling in 2016 also came from automotive electronics, which accounted for 41% of its total revenue; STMicroelectronics' revenue was provided by the Automotive and Discrete Products Division, accounting for 40.34 of its total revenue. %......
Moreover, major semiconductor manufacturers are actively deploying, for example, Qualcomm, which is in the consumer electronics market, is entering the automotive electronics market by acquiring NXP Semiconductors; Taiwan’s MediaTek announced its growing growth in early December 2016. In the automotive electronics market, there are also some strategic mergers and acquisitions in order to maintain its market position, such as the acquisition of Fairchild by Anson, to complement its shortcomings in medium and high voltage power devices; Renesas to consolidate its automotive electronics through the acquisition of Intersil The status of the market.
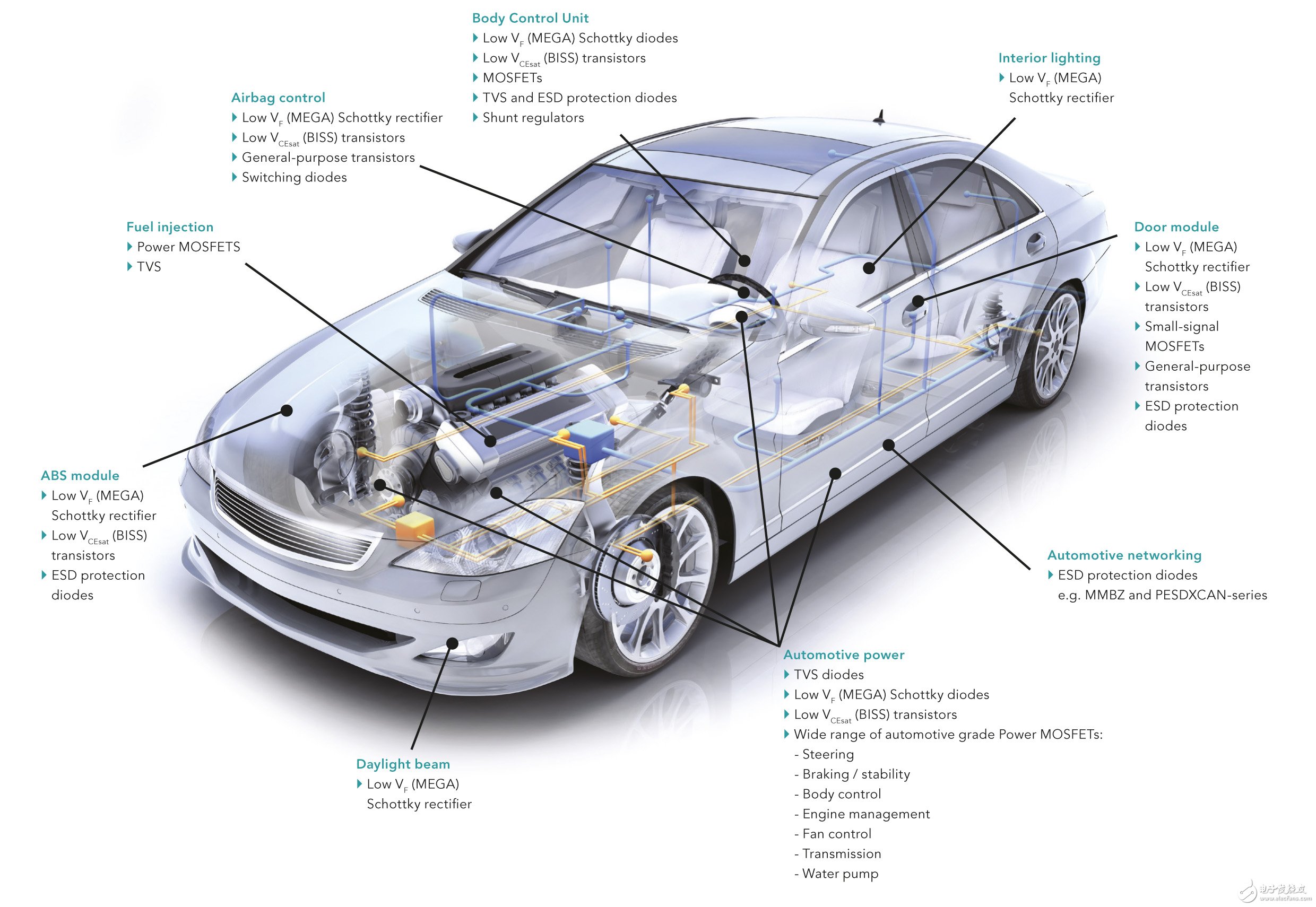
Regardless of whether automotive electronics will truly “take the bar†in the consumer electronics market, it is foreseeable that the automotive industry is moving toward smart, electronic, etc. According to statistics, the proportion of automotive electronics in the cost of complete vehicles is increasing, compact In the car accounted for 15%, mid-to-high-end cars accounted for about 28%, hybrid vehicles accounted for 47%, and pure electric cars accounted for 65%. Under the trend of intelligent and electronic, this will give The entire semiconductor market brings new vitality and new growth points. This article focuses on the current state of the art of power electronics in automotive electronics, the future direction of development, and the challenges and coping strategies that may be encountered.
The development trend of power electronic devices in automobilesAs cars become more intelligent and electronic, the demand for sensors, MCUs, ECUs, IGBTs, and BMS chips is growing. Undoubtedly, among these chips, power electronic devices are absolutely dominant, so what kind of development trend will future power electronic devices show in automobiles?
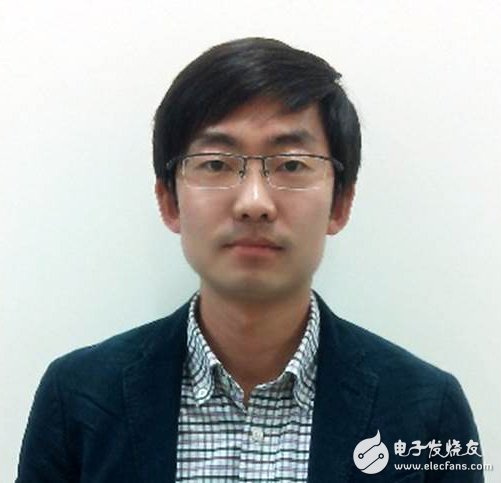
Figure 1: Liu Wenxin, Deputy Senior Manager, Technology Department, Toshiba Electronics (China) Co., Ltd.
“I think there are four main development trends, namely high reliability, high integration, high power and productivity.†Liu Wenxin, deputy senior manager of the technology department of Toshiba Electronics (China) Co., Ltd. said.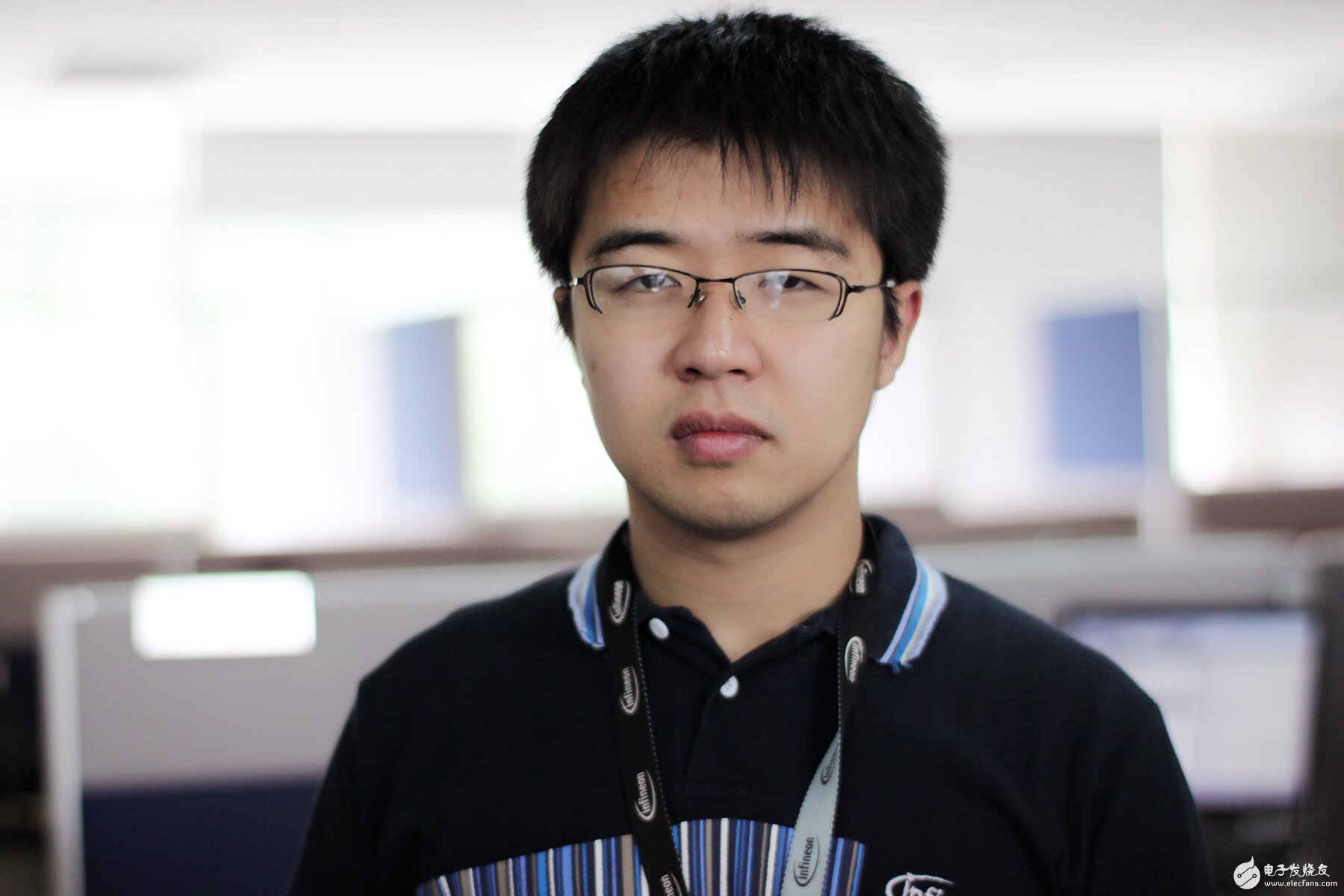
He Yaohua, a power electronics application engineer at Infineon's new energy vehicle, recognized Liu Wenxin's judgment, but he also added the following points.
First, dedicated automotive-grade power electronics will appear in the future. He explained that although automotive-grade certified electronic components are the default entry conditions for automotive manufacturers, automotive-grade certified products have higher reliability and performance, but general-purpose power electronics designed for industrial applications have not kept pace. The development of new energy vehicles with ever-changing needs has been made. The design has already passed the initial stage of “will be usedâ€, and refined design has become a trend and inevitable.
The second is platform design. The development of a typical automotive electronic system takes two to three years. If there are newer requirements in the future, it will take a lot of development cost and time to start the development. If power electronics can be platformized, development costs and cycles can be significantly reduced. He Yaohua took Infineon's Hybridpack drive family example as an example. "For the 70Kw~150Kw platform, the high-end products that can be used in the early development can use the Hybridpack drive pinfin version, so that 90Kw~150Kw, if there is 70Kw~90Kw demand, just need to Replace the power module with the Hybridpack drive flat without changing the circuit and software."
The third is intelligent and functional safety design. Power electronics is traditionally a passive actuator that acts after receiving an instruction. He Yaohua believes that the future trend is not only simple receiving instructions, but also some judgment and protection functions. "For example, adding current and temperature sensors inside the IGBT. When the system may fail, you can make a preliminary judgment. You can try to reduce the vehicle first. Output torque and speed instead of direct shutdown. The battery voltage is high, reducing the switching speed of the power device, protecting the switching circuit safety, and doing the most efficient switching action when the battery voltage is normal." The intelligentization of the power device allows electronic control The system reaches a higher level of security.
Challenges for semiconductor manufacturersAutomotive applications are different from traditional industrial drive applications. He Yaohua said, “The most important characteristics of power converters for generators and transmission and distribution of large hydropower stations are high reliability and high performance, because the value of a single unit is high and the quantity is small. The higher cost of the device is also acceptable. However, automotive applications are high-end industrial consumer goods that are mass-produced. The end customer is an individual and needs to better control the price of the terminal. Therefore, higher requirements are placed on component costs."
Although the cost is strictly controlled, the reliability of the most safety-related products cannot be reduced. Low cost and high reliability are contradictory, and this power semiconductor manufacturer has put forward higher requirements.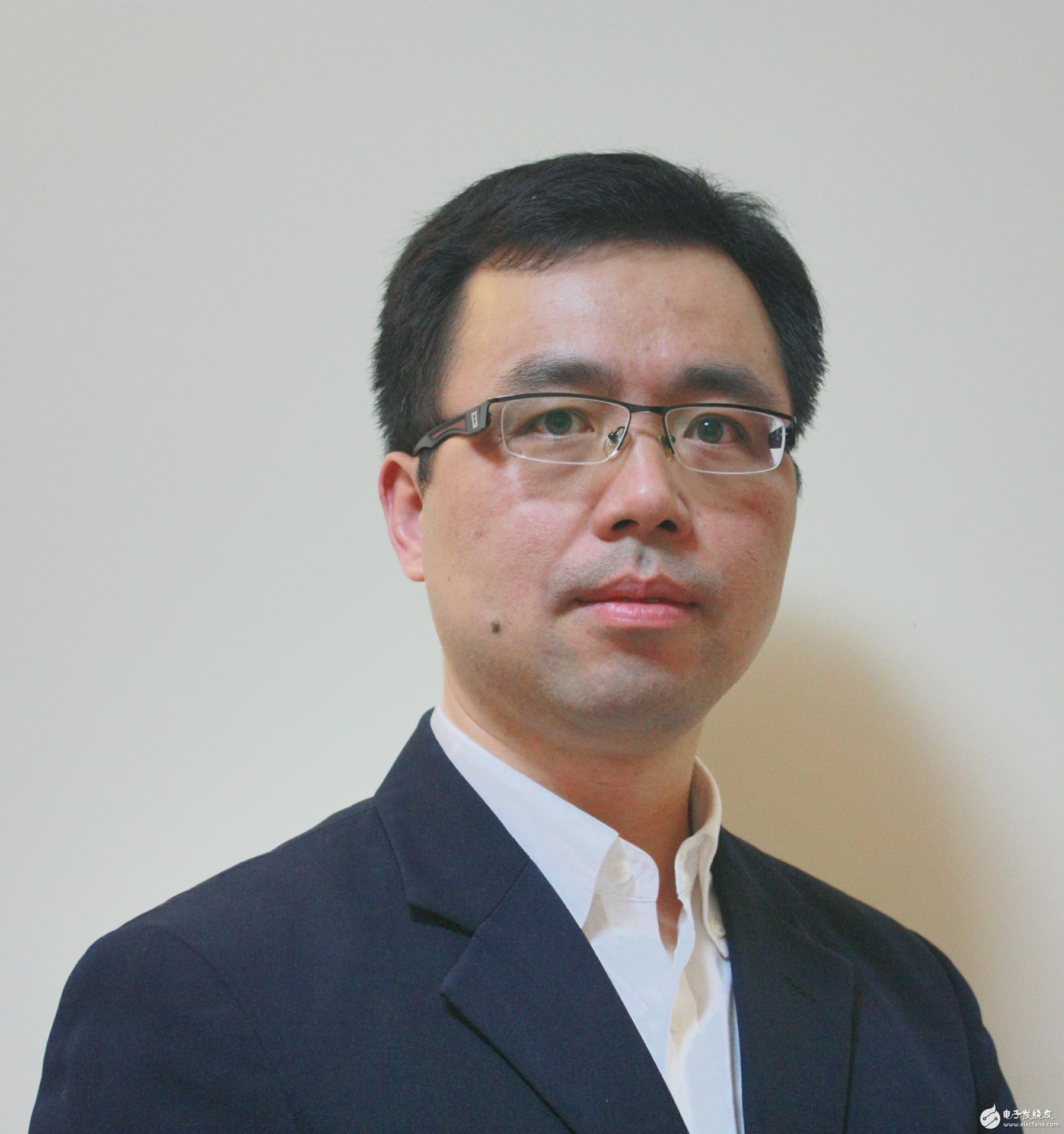
In this regard, Chen Lizhen, senior manager of ON Semiconductor China Solution Engineering Center (SEC), shares the same feeling. "The reliability, energy efficiency and cost performance of power electronics are the challenges faced by power semiconductor manufacturers." For example, in order to increase the cruising range, the inverter needs very high efficiency. At the same time, the device should also ensure high reliability when operating under high temperature and high current conditions.
In addition to these, Toshiba Electronics' Liu Wenxin believes that for power semiconductor manufacturers, the development of automotive semiconductor materials, process improvement, and production quality control are also a big challenge.
preventive solutionFaced with these challenges, different power semiconductor manufacturers have different strategies to deal with them, some improve their production processes, some use new materials, and some respond by changing the package.
According to Chen Lizhen of ON Semiconductor, in order to ensure the high reliability of high current and high power devices, at the device level, ON Semiconductor focuses on new technologies to reduce the conduction loss and parasitic parameters of power devices, thereby improving energy efficiency and Enhancing system reliability, they also invest heavily in new advanced package designs such as TO-Leadless (TOLL), 4-pin TO-247, DSC (double-sided cooling). Compared to traditional packages, these new packages offer lower thermal resistance, smaller parasitics and a reliable structural design to meet the critical requirements of automotive applications.
He also stressed that all of these devices from ON Semiconductor are rigorously tested by AEC certification, such as high temperature reverse bias (HTRB), power cycling, and more. Chen Lijun also specifically mentioned, "Our manufacturing and quality control processes also meet the needs of the industry's reliability and durability."
Toshiba is tackling the challenge through continuous innovation in power semiconductor wafer processing and package types. Its low on-resistance (UMOS 9 generation), high heat dissipation package (copper connection, DSOP double-sided heat dissipation), high integration and other features can help customers achieve high-power load controller miniaturization design.
For Infineon's response strategy, He Yaohua mentioned four points.
First, continue to update the product line to provide more competitive products. For example, he said that Hybridpack2, a power semiconductor module for 120Kw to 150Kw inverters, is widely used in China. The updated version of Infineon's product: HybirdPack drive, maintains output power by optimizing wafer performance and internal package design. In the case of a change, the volume is reduced by 30%, that is, the power density is increased by 30%, because the use of fewer wafers and the reduction of the radiator area, the market competitiveness is also greatly improved.
The second is to optimize the semiconductor process and reduce costs. While most semiconductor manufacturers are still using 8-inch wafers to produce IGBT wafers, Infineon is one of the few semiconductor manufacturers in the industry to use 12-inch wafers to reduce the cost of IGBT wafers by increasing the efficiency of wafer dicing, 12 inches. Wafer means that the number of wafers to be cut per disk is more, and the control rate of yield is higher. How to improve the production yield is also the core competitiveness of Infineon.
The third is to customize IGBT wafers for automotive applications. Previous IGBT wafer design main input sources were industrial applications, such as 650V and 1200V IGBT for 220V and 380V AC rectified output. Infineon's start-up for automotive applications, for 144V mid-mix, 336V to 500V high-voltage hybrid and pure electric vehicles, introduced 400V and 750V wafers, of which EDT2-type chips, the industry's highest product performance, compared to before The product has improved performance by 20%, making a more compact design possible. Of course, all wafers can meet the stringent conditions of automotive-grade certification.
The fourth is large-scale continuous supply capacity and quality assurance. Infineon has two fully automated production lines in Walstein, Germany, specializing in the production of automotive-grade power electronic IGBT modules to ensure adequate production capacity. The fully automated production line also completely avoids the impact of human error. A variety of production quality control systems, and factory products have been 100% coverage test, to minimize the failure rate of the factory products.
He also mentioned that the automotive-grade design and certification system is a guarantee for the high reliability of its products. He Yaohua took the latest HybridPack drive IGBT Module as an example. “The module has been in production for three years from the design concept to the production line. 18 months of this is the reliability verification R&D. The main work of reliability verification R&D is Accelerated aging verification is performed using various limit tests. For example, one of the tests is called temperature cycle test. The IGBT module needs to be heated from 50 degrees to 150 degrees in 5 seconds, and 60,000 times without lifetime decay. The standard of vibration test is also 5g increased to 20g, and can withstand 50g impact in a short time (11ms). At the same time, the HybridPack1 module produced in 2008, after the vehicle runs 200,000 kilometers, the inverter is disassembled and the power module is sent to Infineon. Ling does analysis, basically intact, and can pass the factory test process."
Advice for automotive engineersIn the view of He Yaohua of Infineon, automotive electronics engineers need to pay attention to the following technical characteristics when selecting power electronics.
First of all, there is no doubt that it is necessary to select automotive electronically certified power electronics, and the reliability of the system must be guaranteed from the beginning of device selection;
Second, the overall system design optimizes power device selection and reduces cost. For example, by matching system design and working condition design, optimizing control software according to vehicle operating conditions, reducing power device requirements, improving system performance and reducing costs;
The third is the design and selection of electrical parameters. This requires consideration of the effects of electrical parameters under extreme operating conditions and is verified by simulation and experimentation.
The last point is also the most important reliability design. Failure analysis and endurance testing are required.
His suggestion is to consider reliability and longevity at the beginning of the design, through simulation and experimental verification, and the need to properly design reliability parameters, should avoid excessively high design margins to bring excessive costs.
Anson's Chen Lizhen suggested that when engineers select power electronics, the first consideration is electrical performance, including conduction and switching performance, safe working area (SOA). Although there are many new technologies and devices in the industry. For example, gallium nitride (GaN) MOSFETs have lower switching losses, but engineers should pay more attention to the driver technology of this new device.
Another factor that needs to be evaluated is parasitic parameters, as this will result in additional stress on the device and affect EMI performance.
In addition, engineers should also pay attention to thermal design and system structure. Because in automotive applications, working conditions are very harsh, engineers should consider all conditions to ensure that the system can work in the worst case.
“Engineers should calculate and evaluate the overcurrent capability, temperature rise parameters and switching noise of the power device according to the design requirements of the system in advance to avoid major technical difficulties in testing the later schemes.†Toshiba’s Liu Wenxin Advice to the engineer.
He chose the example of power electronics for new energy vehicles. Compared with traditional vehicles, the energy efficiency and mileage of new energy vehicles are more prominent. Therefore, when selecting devices, not only the performance and reliability of the devices should be paid attention to. It is also necessary to strictly control the static power consumption, low operating voltage, and unit weight of the device.
Disclaimer: The electronic reprinted works of E-Commerce Network are as far as possible to indicate the source, and all rights of the owner of the work are not transferred due to the reprint of this site. If the author does not agree to reprint, please inform the site to delete or correct it. Reprinted works may be subject to change in title or content.
Ceramic capacitor (ceramic capacitor);Ceramic condenser) is also known as porcelain capacitor or monolithic capacitors.As the name implies, ceramic dielectric vessel is a ceramic capacitor with dielectric material.According to different ceramic materials, this kind of capacitor can be divided into low-frequency porcelain dielectric vessel with capacity of 1-300 pF and high-frequency porcelain dielectric vessel with capacity of 300-22 000 pF.According to the structure type classification, can be divided into picture capacitor, tubular capacitor, rectangular capacitor, chip capacitor, piercing capacitor and so on.
Ceramic Capacitor,White Ceramic Capacitor,Smd Ceramic Capacitor,Multilayer Chip Ceramic Capacitor
YANGZHOU POSITIONING TECH CO., LTD. , https://www.cnchipmicro.com